استنلس استیل ترکیبی از عناصر مختلف برای افزایش مقاومت در برابر خوردگی فولاد است. عنصر اصلی آلیاژی در تمام فلزات استنلس استیل کروم است (حداقل 10.5٪). رایج ترین نوع استنلس استیل، فولاد زنگ نزن آستنیتی است که دارای گریدهای 304 و 316 است. این محدوده به دلیل داشتن مقادیر بالای کروم همراه با نیکل به دلیل مقاومت بالا در برابر خوردگی شناخته شده است. استنلس استیل فریتی دومین محبوب ترین است. این شامل فولادهای ضد زنگ درجه 430 است. در حالی که این محدوده با مقاومت به خوردگی فولادهای آستنیتی مطابقت ندارد، یک جایگزین مقرون به صرفه است و اغلب در صنعت پذیرایی استفاده میشود.
فولادهای مارتنزیتی دارای محتوای کروم کم هستند، بنابراین مقاومت به خوردگی پایینی دارند اما دارای استحکام بالایی هستند. فولادهای مارتنزیتی برای کاربردهایی که نیاز به استحکام باورنکردنی دارند ایده آل هستند.
اصطلاح استنلس استیل به طیف گسترده ای از گریدهای فلزی اشاره دارد که حاوی آلیاژی است که حداقل 10.5 درصد کروم دارد. محبوب ترین گریدهای استنلس استیل 304 و 430 هستند. هر یک از گریدهای مختلف استنلس استیل حاوی عناصر آلیاژی مختلفی است که به خواص آن مانند مقاومت در برابر خوردگی، استحکام و انعطاف پذیری کمک میکند.
از آنجا که این ماده ارزان قیمت است، ظاهری عالی دارد، مقاومت بالایی در برابر خوردگی دارد و استنلس استیل بادوام آن بسیار محبوب شده است و در کاربردهای مختلف یک ماده ترجیحی است. استنلس به سادگی به معنای لکه نشدن فلز است. این ویژگی ارزشمند نتیجه افزودن عنصر آلیاژی کروم است که با اکسیژن موجود در هوا واکنش میدهد و لایه ای از اکسید کروم را تشکیل میدهد که از سطح فلز محافظت میکند. اگر خراش یا تماس با مواد شیمیایی تهاجمی لایه را از بین ببرد، به محض اینکه فلز دوباره در معرض هوا قرار گرفت، خود را ترمیم میکند و یک پوشش محافظ ثابت روی فولاد ایجاد میکند.
قابلیت جوشکاری استنلس استیل
قطعات فولادی استنلس استیل که جوش داده میشوند باید بدون لک باشند. هر گونه رطوبت و آلاینده های آلی مانند روغن، رنگ، گریس، چسب یا صابون را حذف کنید. با استفاده از برس ها و ابزارهایی که روی فولاد گالوانیزه استفاده نشده اند و برای کار بر روی استنلس استیل استفاده میشوند، از آلودگی روی جلوگیری کنید. روش های جوشکاری قوس الکتریکی به طور خاص اغلب در جوشکاری استنلس استیل استفاده میشود.
برای جوشکاری قوس فلزی محافظ، دو نوع اصلی پوشش الکترود وجود دارد. اینها نوع آهکی هستند که با پسوند 15 و نوع تیتانیوم مشخص شده با پسوند 16 مشخص شده اند. الکترودهای نوع آهکی فقط با الکترود جریان مستقیم مثبت (قطبیت معکوس) استفاده میشوند. الکترود پوشش داده شده با تیتانیوم با پسوند 16 را می توان با جریان متناوب و با الکترود جریان مستقیم مثبت استفاده کرد. هر دو پوشش از نوع کم هیدروژن هستند و هر دو در همه موقعیت ها استفاده میشوند.
با این حال، نوع 16 نرم تر است، جذابیت جوش بیشتری دارد و در موقعیت مسطح بهتر عمل میکند. الکترودهای نوع آهکی مقاومت بیشتری در برابر ترک دارند و برای جوشکاری خارج از موقعیت کمی بهتر هستند. عرض بافت باید به دو و نیم (2.5) برابر قطر سیم هسته الکترود محدود شود. الکترودهای سرپوشیده برای جوشکاری قوس فلزی محافظ باید در دمای معمولی اتاق در منطقه خشک نگهداری شوند. این پوشش های الکترود، از نوع کم هیدروژن، مستعد جذب رطوبت هستند. هنگامی که جعبه الکترود باز شد، الکترودها باید تا زمان استفاده در یک جعبه خشک نگهداری شوند.
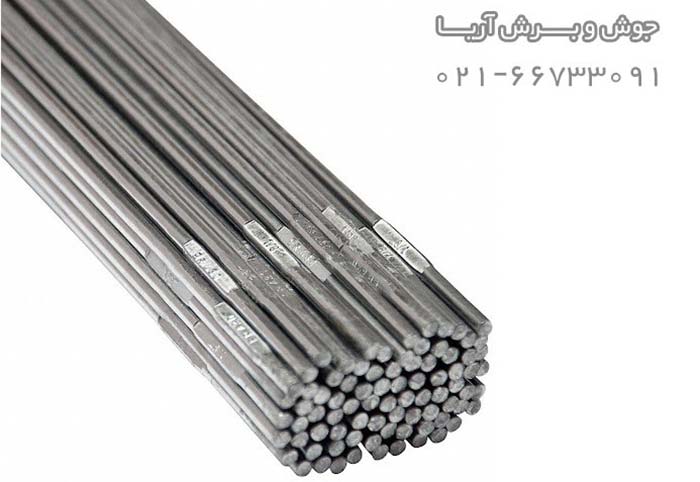
فرآیند جوشکاری قوس تنگستن که به جوشکاری TIG نیز شناخته میشود که با بکارگیری فیلر یا تیگراد استیل به طور گسترده ای برای مقاطع نازک تر از استنلس استیل استفاده میشود. تنگستن 2% توصیه میشود و الکترود باید به صورت مخروطی آسیاب شود. آرگون معمولاً برای محافظ گاز استفاده میشود. با این حال، مخلوط آرگون-هلیوم گاهی اوقات برای کاربردهای خودکار استفاده میشود.
فرآیند جوشکاری قوس فلزی گاز به طور گسترده برای مواد ضخیم تر استفاده میشود زیرا فرآیند جوشکاری سریعتر است. حالت انتقال پاشش برای جوشکاری در موقعیت مسطح استفاده میشود و این نیاز به استفاده از آرگون برای محافظ با اکسیژن 2 یا 5 درصد یا مخلوط های خاص دارد. اکسیژن به تولید اثر مرطوب کنندگی بهتر در لبه های جوش کمک میکند.
انتقال اتصال کوتاه را میتوان روی مواد نازک تر نیز استفاده کرد. در این مورد از محافظ CO2 یا مخلوط 25% CO2 به اضافه 75% آرگون استفاده میشود. مخلوط آرگون-اکسیژن را میتوان با سیم های الکترود با قطر کوچک نیز استفاده کرد. با سیمهای الکترود کم کربن اضافی و محافظ CO2، مقدار جذب کربن کمی افزایش مییابد. این باید با عمر مفید جوش مرتبط باشد. اگر مقاومت در برابر خوردگی عامل اصلی است، گاز CO2 یا مخلوط CO2-آرگون نباید استفاده شود.